Troubleshooting Common Issues with Rotary Airlock Valves
2025-07-03
Overview
Details
Before diving into troubleshooting, it's important to understand what rotary airlock valves are and how they function. Designed to control the flow of bulk materials while maintaining pressure differentials, rotary airlock valves feature rotating vanes that create a seal between the inlet and the outlet.
Applications of Rotary Airlock Valves
Rotary airlock valves find applications in various industries, including:
- **Food and Beverage**: Used for controlling the flow of powders and granules.
- **Pharmaceuticals**: Ensuring accurate dosing and handling of sensitive materials.
- **Chemical Processing**: Managing bulk materials safely and efficiently.
- **Wastewater Treatment**: Regulating the flow of sludge and other materials.
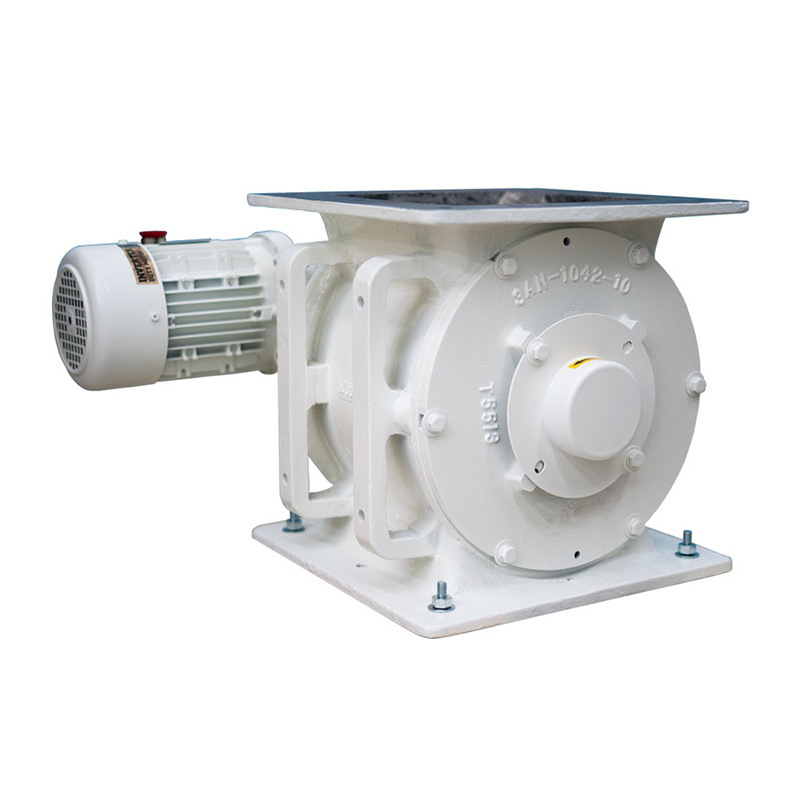
Importance of Proper Functioning
Maintaining the proper function of rotary airlock valves is crucial for preventing downtime, ensuring process efficiency, and minimizing maintenance costs. A malfunctioning valve can lead to material leaks, blockages, and increased wear on equipment.
Common Issues with Rotary Airlock Valves
Despite their robust design, rotary airlock valves can experience various issues. Here are some of the most common problems encountered in operation:
1. Jamming or Sticking
**Symptoms**: The rotor may not move freely, causing material blockages.
**Causes**:
- Material build-up inside the valve.
- Wear on the rotor or side plates.
**Solutions**:
- Regular cleaning and maintenance of the valve.
- Inspecting the rotor and side plates for wear and replacing them if necessary.
2. Air Leakage
**Symptoms**: Unintended air flow can disrupt processes and lead to inefficiencies.
**Causes**:
- Worn seals or gaskets.
- Misalignment of the valve components.
**Solutions**:
- Replacing worn seals and gaskets.
- Ensuring proper alignment during installation and maintenance.
3. Excessive Wear and Tear
**Symptoms**: Increased noise levels, reduced efficiency, and material leaks.
**Causes**:
- Improper material selection for the application.
- Inadequate lubrication.
**Solutions**:
- Selecting materials that are resistant to wear for specific applications.
- Implementing a regular lubrication schedule to reduce friction.
4. Overloading
**Symptoms**: The valve may struggle to handle the required material flow, leading to operational inefficiencies.
**Causes**:
- Incorrect sizing of the valve for the application.
- Sudden changes in material flow rates.
**Solutions**:
- Conducting a thorough evaluation of the required specifications before installation.
- Adjusting flow rates gradually to avoid overloading.
5. Temperature Fluctuations
**Symptoms**: Changes in material properties can lead to clogging or inefficient flow.
**Causes**:
- Inadequate thermal insulation.
- External temperature variations affecting the material.
**Solutions**:
- Investing in proper insulation or heating solutions for the valve.
- Monitoring temperature levels to ensure a stable environment.
Step-by-Step Troubleshooting Guide
Now that we have identified common problems, we can address them systematically. Here’s a troubleshooting guide to help you diagnose and resolve issues with rotary airlock valves.
Step 1: Observe the Symptoms
Carefully observe the valve's operational behavior. Note any unusual sounds, flow disruptions, or performance declines. Documenting these symptoms will help narrow down potential issues.
Step 2: Conduct Visual Inspections
Perform a thorough inspection of the valve. Look for signs of wear, misalignment, or material build-up. Pay particular attention to the rotor, seals, and any other moving parts.
Step 3: Check for Proper Installation
Ensure that the valve is installed correctly according to the manufacturer's specifications. Misalignment can lead to many issues, including air leakage and excessive wear.
Step 4: Test for Air Leaks
To identify air leaks, you can use a soap solution around the seals and gaskets. If bubbles form, you may need to replace the affected components.
Step 5: Assess Material Characteristics
Evaluate the materials being handled by the rotary airlock valve. Consider factors such as moisture content, particle size, and flow characteristics, as these can influence valve performance.
Step 6: Implement Maintenance Practices
Regular maintenance is crucial for optimal valve performance. Implement a schedule for cleaning, lubrication, and parts replacement to minimize the risk of issues arising.
Preventive Measures to Enhance Longevity
To avoid encountering common issues with rotary airlock valves, consider implementing the following preventive measures:
Regular Maintenance Schedule
Establish a routine maintenance schedule that includes inspections, cleaning, and parts replacement. This proactive approach can significantly extend the lifespan of your valve.
Proper Training for Operators
Ensure that personnel operating the rotary airlock valves are adequately trained. Familiarity with the equipment and its function can help prevent operational mistakes that lead to issues.
Use High-Quality Components
Invest in high-quality materials and components designed for your specific application. Using subpar materials can result in premature wear and frequent failures.
Monitor Performance Metrics
Regularly monitor performance metrics such as flow rates, pressure differentials, and noise levels. Establishing a baseline can help identify deviations that signal potential problems.
Engage with Experts
Consulting with manufacturers or experts in the field can provide valuable insights into maintaining and troubleshooting rotary airlock valves.
Troubleshooting common issues with rotary airlock valves is essential for maintaining efficient operations in any industrial setting. By understanding the common problems, employing effective troubleshooting techniques, and implementing preventive measures, you can enhance the performance and longevity of your rotary airlock valves. Regular maintenance, proper training, and quality materials will mitigate the risks of malfunction, ensuring that your processes run smoothly and efficiently.
Key words:
Previous:
Related BLOG
Contact Us
Contact:
Gabrielle Zhang
E-Mail:
WhatsApp:
+86-19398142392
Mobile:
Address:
North of Jiaozhou West Road, East of Xuanzhou Road, Jiaozhou City, Qingdao City, Shandong Province, China